MEMA Aftermarket Suppliers on 2025 and Why Shops Need to Prioritize ADAS
Braxton Critcher [00:00:05]:
This is Automotive Repair News Today. Thanks for checking out this podcast or video. I'm Braxton Critcher and we're talking 2025 technology training in the automotive repair aftermarket. And I'm excited that you're here. I've got some new friends with me, so I know a couple of them, Chris Gardner and Ryan Coinman, but I don't know the other guys. So I'm going to leave it to Chris to introduce the rest of the folks here. So what's up, Chris? Thanks for coming on and introduce me and the listener and viewer to the other friends we got.
Chris Gardner [00:00:42]:
Yeah, we'll do that. Braxton, thanks for having all of us. And we're really looking forward to this and discussing a critical issue and some really neat developments that MEMA has. I'll introduce the topic in a second, but we do have with us today Jim Fish, who is managing the tech training hub. We'll talk about today and the brand new MEMA Training Council for mema. And Scott Brown's with us. He's the founder of Diagnostic Network. He also owns Service Center, Auto Service Center.
Chris Gardner [00:01:19]:
That's fantastic. And then we've got Drew with us. Drew is the content and curriculum manager for Drives Garage Guru, also really involved with ase. And of course you mentioned Ryan. Ryan Coinman is with Standard Motor Products. He's also, he's on the board of ase. So and, and I'm Chris Gardner with mema, MEMA Aftermarket Suppliers and Braxton just to get us kicked off. And I'm going to turn this over to the guys.
Chris Gardner [00:01:52]:
They know what they're talking about a lot more than I do. MEMA Aftermarket Suppliers exclusively represents the leading suppliers of parts, chemicals, tools, equipment and technologies for the vehicle lifecycle industry. And so our members create much of the technology and the information and the education that's consumed by the repair community. And we're very member driven, very member centric. And so our members input and the results of a major research study that we might mention in a minute that we conducted about three years ago, they led to the creation of this tech training hub that we're going to talk about today that we're going to describe. It's brand new and it's exciting. So with that, hey Jim, you had a lot to do with managing the entire process of how this came about. So why don't you tell us just real briefly how it came about.
Jim Fish [00:02:52]:
I don't know how briefly I can do it, but Chris mentioned, Chris mentioned a study that was published three years ago it was, it's in April of 2022. It was conducted in the fall and early winter of 2021, 2022, it was done at the University of Michigan with students from the university. They were talking to a lot of shops. We're doing a deep dive on adas as an advanced technology and how it's impacting the service markets. And we looked in depth at it and we came out with a forecast that was quite eye opening that said that this is going to be some profound change coming up. And as these vehicles hit the park and as these vehicles begin to get in accidents and as these vehicles begin to hit the service bays. And we found that the industry was struggling to adapt and in many cases just outsourcing this stuff back to the dealership and not keeping the work in house. And it led to a number of different, what we call problems worth solving.
Jim Fish [00:03:53]:
And we identified three. And one of them was the preparedness of the shop to repair and service these vehicles. And that led to an exploration amongst the members around training. And it led to a mission statement of a key group of professionals that formed a board of professionals really of which Ryan and Drew were part of. And it would be how might we collaborate to really better the technical readiness of the shops to service these advanced vehicles when they come in in the context of training and over a number of sessions and meetings and workings. And it all resulted in the tech training hub becoming a reality, which is the elevator pitch for the tech training hub is the Expedia for automotive training. And that is you can go and you can learn. Just like if you go to Expedia and you find, hey, I'm going to Vegas and you can see how much is American and Delta and JetBlue and fill in blank here, all these airlines or hey, I might need a hotel and it'll give you all the hotels on one page and their price.
Jim Fish [00:05:06]:
But to book that hotel, you're gonna often leave and go or to book that airfare, you're gonna leave Expedia and go book that airfare directly with the airline. That's much the case here. You can look at, hey, I'm studying for this ASE certification test and here are the training that's available to me by participating MEMA members and I can select the training that's best for me and then I'll go to their environment. So if you choose, say a garage gurus class, you'll click through to that. You will go into the garage gurus environment. If you choose a SMP Class, you will exit the tech training hub and you will go to where that training is. And why is this important? Well, I think hopefully Scott, as a shop operator and still, as you can tell with his attire today, very much a turning wrenches manager, as I call it, why is this important? And from the ADAS perspective, the preview of another report that MEME is going to publish, it's going to say that collision has really been transformed by the appearance of adas in the collision bay. And the calibration and service activity at ADAS has doubled in just the last three and a half years.
Jim Fish [00:06:24]:
However, it's now going to. The growth is going to slow and these are going to begin to show up in mechanical shops now. And the report forecast a growth rate of service in the mechanical shops of 13.5% over the next 10 years. So the ADAS servicing activity is going to just explode in the mechanical sector and it's just reaching the peak growth in the coming years. And in fact, the forecast additionally says in 2031, the repair activity in the mechanical sector will exceed the repair activity in the collision sector. And if you think about all the other technologies that have rolled through from ABS to OBD 2, and it all started in the collision and then mechanical ends up being the bulk of it over time. And that time is sooner rather than later for adas. So that's why this remains so important.
Jim Fish [00:07:20]:
And this is one of the biggest transformations that has happened so quickly. People talk about EVs hitting the car park, but this takes. Has a very long tail. It takes a very long time. But ADAS is like here and now and exploding because it's been introduced so quickly. So it's. Why is it more important than ever to get that training, especially in the mechanical space? Because here comes these challenges.
Braxton Critcher [00:07:46]:
I think he did pretty good there, Chris. He did that pretty quickly. That was good. But I like. Okay, I say ados. Is that incorrect?
Jim Fish [00:08:00]:
Yeah, I mean, it's Advanced Driver Assistance System.
Braxton Critcher [00:08:05]:
So is it a DAS or a dos? Maybe.
Jim Fish [00:08:08]:
Maybe it's my Midwest, my Midwest accent.
Braxton Critcher [00:08:10]:
Maybe it's my Southern accent.
Jim Fish [00:08:12]:
I guess Chris.
Braxton Critcher [00:08:12]:
I guess the. The real answer is Chris. How do you say it?
Chris Gardner [00:08:15]:
I say it.
Jim Fish [00:08:17]:
Yeah. Chris also speaks Southern.
Braxton Critcher [00:08:19]:
He does.
Chris Gardner [00:08:23]:
I certainly do. And you hear it both ways, Braxton. I don't know there is a correct way, so.
Braxton Critcher [00:08:28]:
Well, thank you.
Drew Jablonowski [00:08:29]:
Yeah.
Chris Gardner [00:08:30]:
It's a lot better than saying Advanced Driver Assistance Systems every single time.
Jim Fish [00:08:34]:
Yes.
Braxton Critcher [00:08:34]:
Yes, it is. Yes, it is.
Chris Gardner [00:08:37]:
But Braxton, you know that Jim did give a wonderful overview of why we developed this and where we got to, and he mentioned the need for it. And so I'd love to have Scott speak to a little bit to that very point. You know, what. Why do we. Why is this so needed? Why is it so necessary?
Braxton Critcher [00:08:55]:
Yeah. From a shop owner's perspective, too. I'm curious as well.
Scott Brown [00:08:59]:
Yeah. Well, what's interesting here is that, yeah, I, you know, six years ago, I started seeing these signs, right. And I think a lot of. A lot of players in the industry were paying attention. Some were not paying attention, obviously. And, you know, as this technology continues to evolve and like Jim said, this car park is now moving into the. Into the general repair stuff. We're now seeing organic stuff that comes in here with faults that are, you know, on the dash saying, hey, there's the brake guard system or the adapter cruise system isn't working.
Scott Brown [00:09:35]:
And these vehicles are landing in shops today that don't know what that stuff actually means or what's entailed. And I had a call from a local shop a little while ago, and he asked me, he goes, hey, what are you guys doing about all these cameras and radars on cars? I go, well, you know, I've been preaching to the choir here for the last five years, trying to tell everybody to get training. And he's just now, now waking up. It's. It's very important that we are aware of what these systems are in the car and what service impact, what negative impact we could have on those systems if we're not carrying out service procedures properly. So additionally, these consumers are, you know, sometimes in the early systems, they didn't always do. They didn't behave the way that they were. They were expecting.
Scott Brown [00:10:29]:
Sometimes they. They lose a little respect for the way they're working. But these cameras are doing more than just telling the customer that they're not in the lane or they're getting out of the lane. Some of these cameras are now tasked with doing other things like pedestrian detection and have you. So ensuring that we as service providers understand how these systems are operating and what measures are being provided into the vehicle will allow us to communicate effectively to the consumer as well. So I guess the. The big point here is that, yes, shops need to be educated on this and the workforce needs to be educated. And I think we're way behind.
Scott Brown [00:11:14]:
We're behind where we need to be. So I'm happy to hear that, you know, Mima's got this initiative in place and we need to basically be out there screaming from the balconies, telling these People, hey, you need to get up to speed and making sure that these consumers understand how these operate. And one other thing that I've had some pushback from other players in the industry. They're going, oh, there's such a liability issue. Well, these systems are designed to operate the way that they're described in the owner's manual. And so if you read the owner's manual, that is the operational design domain of the systems. And if you're servicing the vehicle properly as per the manufacturer's requirements and putting that vehicle back into service and it's operating the way it's stated in that owner's manual, you're doing everything that you can to put that vehicle back in service. These vehicles are not driving themselves yet.
Scott Brown [00:12:13]:
They're assisting the driver. So the driver is ultimately responsible for safe operation of the vehicle at all times. And shops need to have that mindset to understand how their approach is into providing these other advanced driver assistance system services.
Braxton Critcher [00:12:33]:
Now, Scott, so obviously I've got a lot of repair shop owners listening. Many whom I'm gathering are probably a little behind you in some of this stuff with training and implementing where you're at with ADOS technology. So for that person trying to catch up, what are some of the challenges that you face during that process, but also, what are some of the challenges that you and your techs are facing now that hopefully this mema training will help improve? But what are some of those deals that you're. You're working through as we speak that are hindering you in some ways?
Scott Brown [00:13:11]:
Yeah. Good. So I, you know, again, you know, six, six years or so ago, I go, you know, I want to try to get some training. I went out to try to get training. There really was no training. There were some guys putting stuff together, and I spent a lot of money and I took my text and got into some training, and I just figured out I had to start doing a deep div and figure this stuff out. So I, you know, started developing training. You know, I, I just did a deep dive and tried to figure out, you know, what's computer vision, what are these sensory systems, what are they doing? And, you know, started to learn as much as I could.
Scott Brown [00:13:50]:
Well, now there is training available, but the big, the big. Why? Why do you need to do this? Well, you've got cars that come in for, say, a wheel alignment, you know, tires, wheel alignment, which is a very common, you know, service. And a lot of times at the end of that wheel alignment process, it says, if this car has this system you know, adaptive cruise control or has a camera system, you need to perform this service and you need to make sure that your entire staff, from the front counter to the back shop is aware of what, what these systems are. So that when you're doing that service and you're putting that car back together, you're doing all the right procedures. But more importantly, you need to have that awareness up front, because when that customer comes in and says, hey, I need a tires and a wheel alignment on my Audi vehicle, and you quote your regular service, and you are not aware that this vehicle also needs a radar and a camera calibration after you're done and you find out at the end of that process and you call the customer up and say, hey, we've got to do this other service. That consumer is not going to have a good, you know, that's not a good experience. So we have been coaching and training our, our front staff, and things still fall through the cracks. So, you know, one of the things that we have been proponents of is, hey, I walk our staff out in the parking lot.
Scott Brown [00:15:18]:
I want you to be observant, look at these cars and look at what equipment is on it. A lot of times you can just assess that pretty quickly to see that there's a camera in the, in the window, the windshield. You can see telltale signs if there's a radar. And when you have that awareness and heightened awareness, you're going to be able to deliver a higher level of service to that client and ensure that they, they get the proper service and maintenance on their vehicle.
Braxton Critcher [00:15:46]:
Okay, that makes sense. Chris, what are your thoughts about other things we got to talk about?
Chris Gardner [00:15:52]:
Well, so that's, that's a great perspective from, you know, a progressive leading shop owner. I'd love to hear Drew and Ryan share their perspectives on from a supplier, Parts Elite, both of these companies, top part leading part suppliers for this industry, to share their perspectives on why it's so critical that they get their training out, that the training's professional and that they get it down to the repair folks, repair professionals, and then even comment about how the tech training hub ultimately will help do that. So, Drew, why don't you start?
Scott Brown [00:16:32]:
Sure.
Ryan Kooiman [00:16:32]:
Thanks for having me on. I appreciate it. You know, I was listening to Scott talk there, and I was working on a couple vehicles the other day, and we were actually doing some ADAS calibrations, and one of the things that I found to be interesting was I could recalibrate the vehicle out of specifications. So I actually was able to recalibrate I believe it was the, the camera and I think I also did it with the radar up to 5 degrees off. So if you do the simple math on that, it actually shortens the, the range of that. You know, I think it's like 1 degree per 65ft. So now we're, we're really being detrimental to the system. So part of the, the training to Chris's part is it's not just learning about ADAs, it's, it's learning about how to do it properly.
Ryan Kooiman [00:17:25]:
Right. I mean I could whip through, I did both of the calibrations in probably under 10 minutes, you know, where they should have taken more like 30 minutes, you know, so it's understanding that, you know, slow is smooth, smooth is fast kind of a thing and understanding how to do it right. You know, a lot of these tools are becoming so advanced that you know, you really just have to push some buttons and move stuff into certain directions or certain areas. But if you're not setting them up properly, if you're not taking the time to, you know, do the right measurements, you can set them wrong and the car will drive and they'll drive fine until it comes to that point where that technology is needed to step in and assist and, and that's an issue. And you know, we've my, the training staff that, in the content staff that work for me, you know, they do a lot of hands on at shop so we actually send them out in their downtime now and you know, work with shops and develop case studies in real world content for us. And we found that a lot of the adas problems just comes down to an understanding of basic electrical. So it's not even understanding how to do a calibration, it's, it's understanding just basic electrical. And we find that that's starting to get into, you know, your brakes, your front end, your engines, you know, all facets of the vehicle, even more so in adas.
Ryan Kooiman [00:18:44]:
And it's, it's a challenge, you know, it really is a challenge to try to, to tell somebody who's been doing, you know, working on cars for 20 or 30 years like hey, let's, let's go back to basics, let's, let's figure this out and work our way back from, you know, from there forward. So ADAS training is, is super important. Probably one of the most important things. It's changing. I sat in a room with Ryan at a meeting and a statistic, statistic came out that shop. So I, you know, different size shops said on average about 6 to 7% of them only see ADAS vehicles or vehicles equipped with ADAS equipment. And we looked at each other and we, you know, we kind of chuckled because it's more like they just don't have an understanding of how many vehicles have ADAS equipment or need those ADAS calibrations. So it's, it's definitely interesting.
Braxton Critcher [00:19:38]:
Ryan.
Drew Jablonowski [00:19:39]:
Yeah, so Standard Motor Products has been in business for 106 years now and been primarily dedicated to the aftermarket. And so one of our focuses with training and we actually started our training department in the 1960s. So we've been in this over 60 years now and our focus has been to help maintain the aftermarket. If we don't have aftermarket technicians installing parts, we don't have anybody to sell stuff to. So we're not trying to sell them stuff, but we're trying to keep them in business. And so when we look at training or the reasons for training, I personally kind of put it in four different categories. We've got one like you've heard here already, it's new technologies. Electric vehicles, ADAs, what's the future holding even electronic parking brakes.
Drew Jablonowski [00:20:26]:
Today we see more of those things getting broken on routine brake services. So, so there's advanced stuff. On the opposite end of the spectrum you've got new people entering into the industry and so there's got to be something available for them. Fundamentals, how does tire pressure monitoring systems work? You know, how does ignition systems work? How does fuel injection work? So you've got kind of two ends of the spectrum, but in the middle here you've got the technician that's been in it for a while and trying to advance his career and learn new technologies. Been really good at the fundamentals doing, removing reinstall stuff. Now he's trying to get a little bit more into diagnostics. And then we've also got the, the fourth category is just kind of a good refresher. Somebody's been doing it for a long time.
Drew Jablonowski [00:21:09]:
And I tell you, I still spend probably 50 to 100 years or hours depending on the year attending training that I've already heard before. And it's like, oh yeah, that's right, I kind of forgot about that. And so you know that that's why training is important to really all aspects of the industry here. And so we've been well known in the industry for doing live training for many years. But with accessing Internet and web based training in the mid-2000s, obviously during the pandemic, it drove everybody to step up their game with virtual classes and doing stuff from the studio. And so that's kind of the beauty of this tech training hub. You know, we've always said we've got training when you want it, how you want it, where you want it. And I'm, I'm handcuffed to my categories.
Drew Jablonowski [00:22:03]:
Standard Motor Products makes vehicle control systems and temperature control systems. And so when people go, hey, I want a steering suspension class, well, that's not my category. I've got nothing for you. And so, or what about brakes, you know, friction material or rebuilding automatic transmissions? Well, those aren't my categories, but Drew might have something on that topic. Snap on might have something on that topic. Gates might have something on that topic. Other members of the MEMA Tech Training Hub might have stuff for that. And so kind of back to what Jim was saying earlier, this is kind of your one stop shop or your Expedia for that.
Drew Jablonowski [00:22:44]:
So a technician may be, or a shop owner might be assigning something to one of their new staff members and go, all right, go here, find this fundamental piece because, you know, adas and EV is great, but there's still a lot of people struggling with diagnosing a misfire or evap code or something like that. And so, you know, where do we find training for that? Come to the MEMA Tech Training Hub and you're going to find it from probably five different training providers.
Braxton Critcher [00:23:13]:
Yeah.
Chris Gardner [00:23:18]:
Oh, excuse me.
Braxton Critcher [00:23:18]:
Go ahead, you're good. I'm just curious, you know, this is probably something for you and Jim, but you know, with all this training and some shops not on the same page, trying to get up, you know, to speed and technicians and all this stuff, I, I, for mima, there's, when you're trying to put this, all these trainings online, you know, there's got to be some sort of group of people to sort of be on the same page to help others who aren't. So what, what kind of council or like training council are you guys assembling to help with that? You know, as you, as you grow.
Chris Gardner [00:23:56]:
So, so Braxton, I'll, I'll let Jim describe that in more detail. I think that's, that's a great question because we, as I said earlier, we're member driven. So our members are the experts in a lot of things. And so we're here to facilitate and we are forming a group of individuals that are, who are training executives and trained professionals. We're launching in January the MEMA Training Council to do that very thing to help make sure we're doing the Right things. And to oversee the tech training hub. Jim, you want to go into more detail though, about that?
Jim Fish [00:24:32]:
Yep.
Chris Gardner [00:24:35]:
Jim, you're muted.
Scott Brown [00:24:39]:
Sure.
Braxton Critcher [00:24:39]:
Chris, okay? Yes.
Chris Gardner [00:24:41]:
Yes. You're good.
Jim Fish [00:24:42]:
Nice. Yeah.
Ryan Kooiman [00:24:43]:
Okay.
Jim Fish [00:24:43]:
It's like so. Yeah. So we've had an informal council really for the last two years. And it was important that we all understand what is, what is the objectives of training for MEMO members. And it was pretty surprising in that they were pretty aligned and why did they do training. But it wasn't what you might think. I mean, number one was they want to build their brand, they want a better position in the marketplace, was kind of universal, number one. Number two was in general, they want to sell more parts or more tools that they are a business after all.
Jim Fish [00:25:26]:
Number three, they want a connection to the technician. Because of the way many MEMA members go to market through two, three step distribution, they get so distanced from the working technician and they want a better relationship with that technician, a little bit more direct that training offers. We used to call it belly to belly, if you will. And then lastly, is not universal, but it is a goal of some and that is to be a profit center for the business. But that definitely is not universal. Most in fact, their objective is those top three. Build the brand, sell more parts, have a direct relationship with the technician. And so forming a council will allow to further those goals in a collaborative fashion.
Jim Fish [00:26:18]:
What does that mean? Number one, we constructed this tech training hub and we certainly can't just have MEMA go run a training hub for their members. It really needs to be operated by the members. So there is budget apportioned to it. And now we have something stood up and now what do we do next? What are the. What additional features? Because this isn't what we all envision it can be. It's a very, you know, a minimum viable product. It's the intention is to drive prospective students into these training programs to accomplish these goals. Now what else can we do with it? And that becomes really the one of the roles of this training council.
Jim Fish [00:26:59]:
Number two is help them understand there's a big standard deviation, if you will, about the methods of training and the quality of the training. And you have organizations that have been doing it at scale like Ryan and Drew for literally decades. And they're very honed and polished and they have learning management systems and they're ASE accredited. And then you have other entities that are not so mature. So really it's a great way for those that want to mature their training practices to learn about all in one Place and network with their peers, understand what these best practices might be, even bring in some other outside thought leadership. You know, how does aerospace train their technicians? There's a lot of overlap there's between aerospace and automotive in that they are technicians and the tools they use. Actually some of these come off tool trucks. The secret is I one quick story as I was out riding along in my snap on days on a snap on van and we went to an aircraft maintenance facility.
Jim Fish [00:28:08]:
They had 600 working technicians here and I was like, they don't fix cars here. He goes, watched, he parked his truck, he set up a coffee table and he did not move for eight hours. And 600 techs came to him buying tools. I was like, oh, the overlap is really incredible. So it's, it's what my aerospace be doing, what my other H Vac might be doing. You know, these other for training their people. Can we learn something from other industries, what top technologies are coming about? So it becomes a learning, it becomes a training forum for training managers, if you will. That's really the function and the role of the council in a collaborative fashion.
Jim Fish [00:28:49]:
And then the last piece is, is there research that could be done in collaborative fashion? That there are questions that would help internally, help you get the additional investment to do the next thing you'd like to do for the business. Is there some data that can be gotten in a collaborative fashion to help understand the quantified impacts of training out there? Like one hypothesis I've been running through my head is, you know, how much does a technician earn that's ASE certified versus one that isn't and might that data be motivating to attack? You know, I've been turning wrenches for five or six years in a shop and I'm kind of the brake and suspension guy and I want to make this my career. And then I learn these ASC certified guys make 15 grand more a year than the people that aren't. Well, that's something I should go do, right? Like how do I do that? I need to be trained. So that's some of these data sets that might be helpful for the technician to motivate them to consume training if they aren't already feeling it. You know, talk about wallet. The wallet type impact. So that's really the three prongs of the council is, you know, run the website, get some research and then a collaborative learning environment.
Braxton Critcher [00:30:07]:
Right. So you know, one thing that I'm curious about is 2025 Technology Training ADAS. I had not really thought about the aerospace and automotive, that's, that's pretty neat that, that they're kind of connected in that way, Jim. But when you think about the next 365, the next year, especially with new administration and government for the United States, this new training program and, and all that's going to happen that we're not going to know about, of course, in the next, in the next year you like, obviously we got some catching up to do. You guys have talked about a lot of shops need to do more training, get up more up to speed on some of the technology they have in their shop so they can better serve their customers. But just how far behind are we? And I don't know, you can just chime in whoever has a good answer to this. How far behind are we and how much do you think this training will help? But also, even if you offer the training, how do we get it in front of people and motivate shop owners to understand the importance as to why they got to do it? So I mean that's like a three parter. But I think it's important to discuss as we go into a new year and think about the things we got to do to try and get closer to where we need to be.
Jim Fish [00:31:34]:
I'm just going to make a quick comment, hopefully to offer an intro to what Scott's thoughts are in that I consider the mechanical space of the aftermarket to be a bit behind mostly because of the structure of the industry. If you think about aerospace, for example, you have to have FAA certification to do every job. And FAA certification is, is a very rigorous, training intensive thing to accomplish. So that just on the structure and then when you look at the automotive repair space you have collision and mechanical collision is driven by these MSOs which are, you know, caliber has 1800 shops, they are by far the biggest repair shop count operator in our industry and that continues to consolidate. And when you have corporate ownership, it drives the rigor and training, whereas in general you have shops like Scott's. That's very much up to the owner and what his motivation and aspiration are for his technicians. A guy like Scott will be very dedicated to the career advancement of his 25 year old tech and mentoring him and encouraging him, that becomes mandated in a corporate environment like a collision mso. But there's many independents that view ATTCK as a necessary evil to make money.
Jim Fish [00:32:58]:
So I consider this kind of collaborative approach to be full of impact and we've seen the interest come from the MEMA membership. So I, I'd like to Hear Scott's take on, on these pain points because, because I look at an industry perspective and it's just the, the nature of the structure of the mechanical space which leads it to be a bit of a laggard.
Scott Brown [00:33:25]:
Yeah, I, I, I appreciate those comments. That's really interesting. I, I don't know if I can really formally quantify what percentage of the industry is behind, but I would, I would say along the lines, a lot of it. Right. And you know, Jim brings up a good point. You know, you look at the fact that the faa, right, requires there are certain requirements, right. So mechanic has to be licensed to work on stuff. When they're working on it, it actually gets signed off by an inspection authorization person.
Scott Brown [00:34:02]:
That person has to have continuing education to continue their, their certificate, their, their level of authority. And in our industry we are highly unregulated, which is, is attractive. We have voluntary certification through asp. However, I think that we're going to hit this point here and I'm, I'm projecting that because of all of these advanced features on these vehicles, it's going to put a higher bar on the service requirements in the state of California here. You know, we're highly regulated. We have smog inspections. You have to be licensed, you have to have continuing education, but that's just a small portion of the service. We had a break and light inspection program in the state that just got sunsetted and it's now migrated into a vehicle safety inspection program.
Scott Brown [00:35:00]:
But the only driver to that is if the vehicle is cited for some type of violation or the car has gone through a total, got totaled in a collision and somebody wants to put it back into service and it goes through a salvage title process where it now has to go through this big, this heavier duty vehicle safety inspection program that now gives the inspectors, and I'm one of those inspectors, authorization to fault a vehicle with a, you know, ADAS warning light and that car needs to be fixed in order for it to get its licensing to get back on the street. The missing piece there is that all these cars that are going through a collision cycle, getting repaired and getting, putting back, get put back into service, all the warning lights are out. Maybe there's no DTCs, but that performance, that system may not be 100%. I anticipate us seeing somewhere down the road that we have those vehicles that go through a repair process like that has to have somebody with some credibility credentials performing those services and signing off on, hey, this was performed as per the OEM specific and the vehicle is now operating as, as described in the owner's manual. And, and I take that, you know, I appreciate that FAA thing because I, you know, I got my pilot's license a decade ago, and when I was going through all that training, I said, man, all this, the stuff could be just moved right into our field and we could start applying it and it would be beautiful. And the other thing that I found is that there are other drivers that could incentivize our industry into doing such things. So a lot of these parts suppliers, they would be more interested in having a shop that was highly competent buying their parts so they didn't return parts. Right.
Scott Brown [00:36:59]:
A lot of parts get returned because they're trying to fix a car and they're not. They're just changing parts out. So insurance industry would probably be more appreciative of a shop that really was trained and up to speed. Speed. And so therefore maybe the insurance would give them a benefit. But I think that there's some drivers that we can collectively get our heads together and put some things forward and, and get our, get our focus in, in the right direction and incentivize this training and professionalism so we can deliver what the type of service that these vehicles are actually demanding.
Braxton Critcher [00:37:39]:
What else, Chris? What else we need to talk about?
Chris Gardner [00:37:42]:
I think that that's covers a lot of it. There's so much more to this. Maybe we need some more. Another podcast, practicing the first one. We talked about the need for, you know, identifying when cars need to be calibrated, and we just touched on that in the, in, in this podcast. There's so much more to this topic. One thing I did want to mention, though, Braxton, is that a couple things. One is the tech training hub is there.
Chris Gardner [00:38:11]:
It doesn't offer training. It's a portal to point the repair community to the training offered up by our members. And second, that the industry research and our members drove the development of it. Jim covered that, but it's very important to note that. And third, I don't even think we list we described the, the URL for it. If we didn't, it's mima.org/tech-training-hub. It's that simple.
Braxton Critcher [00:38:45]:
I'll. I'll put a link in the show notes in the description of the video. We can do that. Oh, perfect. That'd be a lot. Yeah, it'd be a lot easier. Yeah, we'll do that.
Chris Gardner [00:38:55]:
That'd be great. So I think we covered all the highlights.
Braxton Critcher [00:39:00]:
Yeah, like I say, yeah, we'll do another one. And every, every little detail that we mentioned, you could record an entire podcast on each detail. So we'll try to break that down at some point. Chris, we'll do it. But this is where you come in. If you're listening or watching this episode. Thanks for doing that. If you watched all the way through, thank.
Braxton Critcher [00:39:20]:
Fantastic. Pat yourself on the back. And this is where you come in, though. This is the important part of why I do automotive repair News today. To keep you informed, to let you know of the future of what's about to happen. I'm not the expert. That's why I have guys that I do on today to help me learn, and hopefully you as well. So in the comments, if you're on Spotify or on YouTube, you can give us your thoughts, opinions about what's been said today and other things that you may have done or found effective for your repair shop and trying to get updated on ados and the struggles that you've had.
Braxton Critcher [00:39:58]:
And that's what this is supposed to be for. A sounding board to share some of those concerns so that we can learn and grow together. So that's where you come in. Do that today. And if you haven't subscribed to the podcast channel or the YouTube channel yet, do that now. You'll get notifications when you hit the bell for new content like this and if you can share the video, that would greatly help the podcast. But it's not selfishly that I want more subscribers or more shares. I just want more people to know about what's happening in the industry.
Braxton Critcher [00:40:29]:
So if you can just share the video or share the podcast on your social media platform of choice, that would be so. So I'd be so thankful for that. So that's where you come in and I encourage you to help out in the industry any way possible. Thanks for checking out this episode. Hey, if you're still here, thank you so much for listening to this episode of Automotive Repair News today. If you enjoyed the show, please take a moment like share. Subscribe to the podcast. It'll help us out a big deal and help grow the show.
Braxton Critcher [00:41:04]:
And you know what, while you're at it, slap on a review too. If you feel like this content is helpful for the industry, don't forget to follow us on all your favorite social media platforms. We're on Facebook, TikTok, YouTube, Twitter, Instagram, LinkedIn, stay connected and be the first to know about new episodes, behind the scene content and more. And until next time, let's make the industry better together.
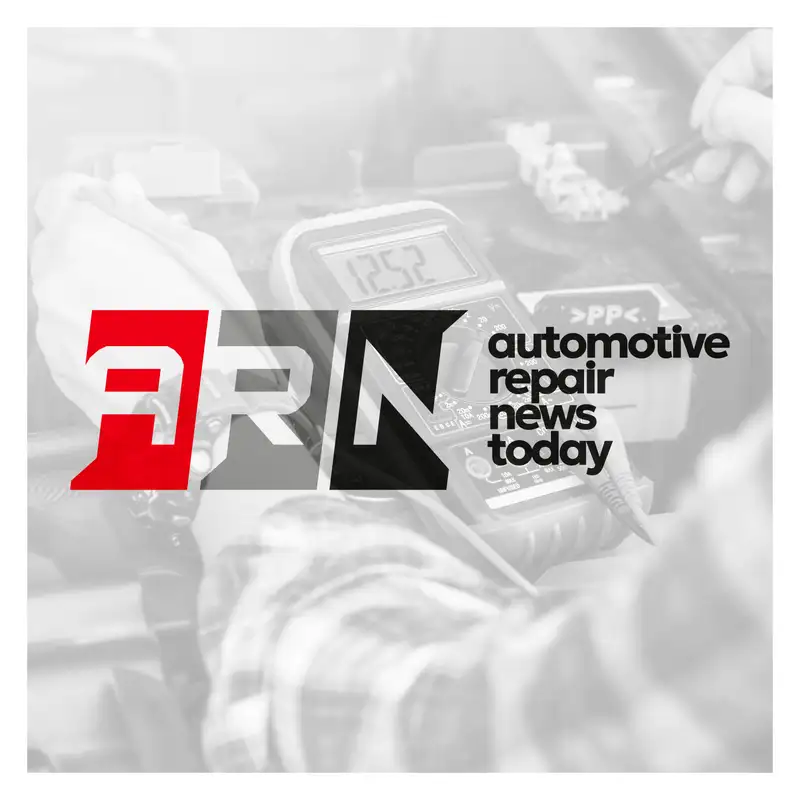